Dry High Speed Machining of Hardened Steel
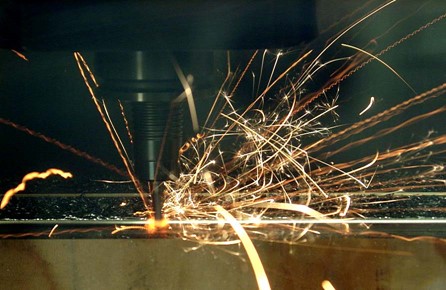
In recent years various publications showed the potential of monolithically grown TiAlN based coatings to protect cutting tools in dry high speed machining. However, the coatings structure and the presence of Ti in the coating formula were seen as weak points because Ti forms a large volume porous titania scale, which is highly permeable for oxygen especially during exposure to high temperature. Furthermore, as the reported coatings were deposited by the Arc Bond Sputtering (ABS) technique, a major drawback was the presence of a large number of growth defects originating from the droplet phase produced in the arc etching step, which further compromised the coating density.
To eradicate these problems a strategy was adopted to develop an Yttrium stabilised, Ti- free nitride based coating utilising nanoscale multilayer structure, where the rare earth element, Y is introduced not only in the bulk of the coating but also in the coating-substrate interface. Furthermore the metals in the coating constitution were selected among these which form dense oxide scales when exposed to high temperatures. Hence CrAlYN/CrN was developed, [1].
The coating utilises nanoscale multilayer structure with bi- layer thickness of 4.2 nm. HIPIMS was selected as surface pre-treatment, and coating deposition technology to avoid the drawback of the other state-of-the- art techniques. The utilisation of HIPIMS discharge in the surface pre-treatment stage of the process not only allowed production of droplets free ionised metal flux but more crucially allowed implantation of Yttrium in the interface, [2]. It has to be noted that unlike Arc evaporation, HIPIMS allowed production of Yttrium ions from an alloyed AlCrY target in a very stable process. The Y stabilised, Ti-free coating formula and the employment of the HIPIMS technology for surface pre-treatment provided the key to enhanced oxidation resistance of the coating.
The synergy between excellent oxidation resistance low coefficient of friction at high temperatures and high hardness, (40 GPa) retention up to 950°C is best demonstrated for CrAlYN/CrN in dry high speed machining operations. In dry high speed milling (Vc =385 m min−1) of hardened A2 tool steel (HRC=58), 8 mm cemented carbide ball nosed end mills coated with CrAlYN/CrN outperformed range of advanced PVD coatings including TiAlCrYN, which is one of the market leading coatings dedicated to this application. When the test was carried out at the higher end of the cutting speed range of 500 m min−1 this difference in performance became even more pronounced where CrAlYN/CrN coated tools showed by factor of 8 longer life time, (download PowerPoint slides for more information (PDF, 822.5KB)).
[1] P. Eh. Hovsepian, C. Reinhard, A.P. Ehiasarian, CrAlYN/CrN superlattice coatings deposited by the combined high power impulse magnetron sputtering technique. Surf. and Coat.Technol. 201(2006)4105-4110.
[2] P. Hovseapian, A. P. Ehiasarian, R. Tietema, C. Strondel, A method for the manufacture of a hard metal coating on a substrate, UK Patent GB 2450950, 19.05. 2010, priority date 02. 01. 2008.